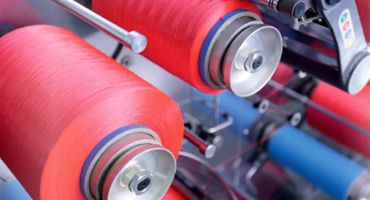
Date: 28 May 2019
Some brands are committed to offering their products without sacrificing their high quality by using largely recycled raw materials in textile products in the years to come. Besides, they work on, with their own supply chains to reduce energy and water consumption in conventional dyeing and finishing processes.
Coloring with the conventional dyeing is preferred by companies especially for production flexibility because very small quantity of color demands can be supplied quickly with this method therefore coloring with conventional dyeing is still an indispensable method for these reasons.
Mass Dyeing is, providing functionality to the yarn or coloring the yarn , through adding additive directly to the melting polymer , at the spinning process. Unlike conventional dyeing, there is no need to use of water in mass Mass dyeing is increasingly getting important with environmental motivations Adding color and functional masterbatches to melting polymer during the spinning production is an advantageous method in terms of both water consumption and reducing the carbon footprint impact. The traditional problem in mass dyeing has always been the lack of production flexibility Small quantity of color demands cannot be supplied quickly. However, this situation is changing because today, flexible processes that can produce yarn with very small lots are commercialized. In addition, both coloring and functional masterbatch production technology is developing.
During the spinning process, various additives can be added and many specifications of the yarn can be developed without the need for finishing.For example using halogen free additives provides permanent flame retardant specifications to the textiles It is requested that the fabrics used in the cinema, hotel and automotive sectors have a certain degree of nonflammability Many nonflammability degrees can be achieved, especially with the addition of masterbatches during polyester-based spinning process This method is more environmentalist because it requires less water usage than conventional dyeing.In addition, the mass dyeing method provides a more permanent fire retardent performance compared to the exhaust or padding applications since the fire retardant additive is integrated between the polymer chains.
Durability of the technical textiles to the external environment conditions can be achieved by mass dyeing. In these applications, additives that absorb detrimental effects can be used during the spinning process to prevent the fabric damage by the sun's harmful ultraviolet rays.
Mass dyeing also have a lot of technical advantages compared to conventional dyeing. For example, coloring with masterbatch by using pigments providing high light fastnesses , 7-8 levels of color fastness can be maintained up to 2000-4000 hours according to ISO 105 B04 test standard.
Leading brands publish projects about they will use only recycled resources, in their production, in the future . Another advantage of mass dyeing is the level dyeing results can be obtained on recycled synthetic yarns dyeing. In conventional dyeing process, most likely recycled yarns will have color differences between the lots because of the uneven dyestuff absorbation, As there is no such problem in mass dyeing, it is thought that the increasing importance of recycling will lead to an increase in demand for mass dyeing in the coming years.
By comparison these advantages of masterbatch production method, the high production flexibility advantage of conventional dyeing is unquestionable therefore conventional dyeing will continue as an indispensable method but masterbatch technologies can also contribute to the sustainability of conventional dyeing. As is known, polyesters can be dyed at 130 C levels In conventional dyeing, the dyeing temperature of the polyesters can be reduced from 130 ° C to 100 ° C by the agency of masterbatch additives which reduce the dye absorption temperature.
Due to the fact that production technology with masterbatch is a sustainable and environmentally friendly approach to the coloration and functionality of textiles, it is expected to see more demand in the coming years.